Our team has extensive experience in aging testing
Medical blood glucose testing equipment PCBA motherboard undergoes up to 500 simulated tests, with an aging temperature of room temperature and a duration of approximately 48 hours
Aging of transportation intelligent high-definition camera motherboard: temperature 60 degrees Celsius, humidity 70%, lasting for 72 hours
Solar energy storage device controller room temperature aging: continuous charging and discharging for 3 cycles, aging time of 24 hours
Room temperature aging of pigsty environmental controller: continuous control and network communication, aging time of 24 hours
The purpose of PCBA aging test
Screening for early failure products: Through aging testing, early failure products caused by various reasons during the production process can be screened to prevent these products from entering the market.
Improving product reliability: Through aging testing, potential issues in product design, materials, and processes can be identified and repaired, thereby improving product reliability.
Evaluate product lifespan: Through aging testing, it is possible to simulate the actual lifespan of the product in use, providing a reference for the warranty period and service life of the product.
The method of PCBA aging test
Room temperature aging test: Conduct long-term stable operation test on electronic products in a room temperature environment. This method mainly tests the performance of the product under normal usage conditions.
High temperature aging test: Conduct operational testing on electronic products in a high-temperature environment. This method can accelerate the aging process of the product and expose potential defects more quickly.
Low temperature aging test: Conduct operational testing on electronic products in a low-temperature environment. This method mainly tests the performance of the product under extreme temperature conditions.
Alternating temperature and humidity aging test: Conduct operational testing on electronic products in alternating temperature and humidity environments. This method can simulate the usage of products in complex environments and comprehensively evaluate the reliability of products.
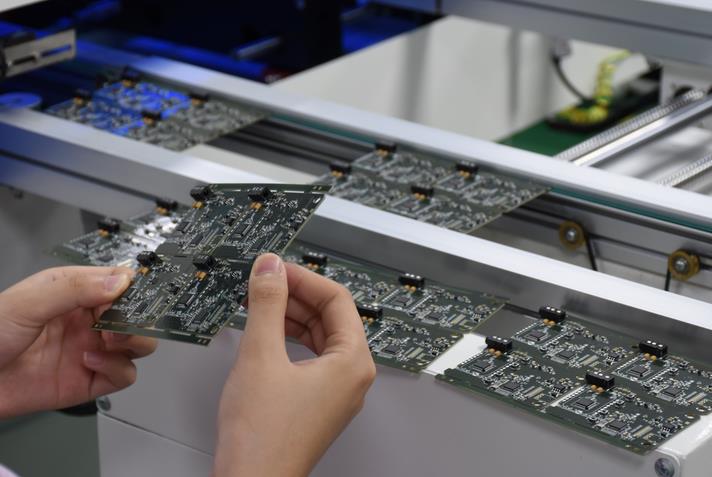
The process of PCBA aging test
Set testing conditions: Based on the characteristics and usage scenarios of the product, set appropriate testing conditions, including temperature, humidity, voltage, etc.
Prepare test samples: Select a certain number of electronic products as test samples to ensure their representativeness and sufficient quantity.
Conduct aging test: Place the test sample under the set environmental conditions for long-term stable operation testing. During this process, it is necessary to closely monitor the operational status and performance of the sample.
Analyze test results: After the test is completed, analyze and process the test data to evaluate the reliability and performance of the product. If potential defects or performance degradation are found in the product, corresponding repairs and optimizations need to be carried out.
Feedback and improvement: Provide test results to relevant departments and personnel for timely implementation of measures for improvement and optimization. At the same time, summarize and share the experience and lessons learned from aging testing, providing reference basis for subsequent product development and production.