DFM inspection
Check the following items in the customer's design PCB, BOM, schematic, and finished product assembly manual:
File version and last update time
Process: Lead/lead-free
Clear component tag numbers and screen printing
BOM containing manufacturer's brand and part number, description, and item number
Confirm PCB production process: material, board thickness, copper thickness, number of layers, surface treatment, character color, and special process
Reasonable PCB layers and splicing methods
Provide the correct SMT patch file
A comprehensive program burning and functional testing plan
Clear finished product assembly manual and schematic diagram
Other special process requirements
New Product Introduction Meeting
Organize sales, engineering, production, procurement, quality and other personnel to hold a new product introduction meeting:
Provide a detailed introduction to the client's project background, product application scope, delivery time, and special requirements
Determine internal customer number and product number
Clarify production batches, procurement, and delivery quantities
Evaluate the process difficulty and key quality control points of the project
Clarify the procurement cycle for PCBs and electronic components
Propose a draft production plan
Preparation of fixtures, fixtures, and auxiliary materials required during the production process
Clarify the testing plan for customer products
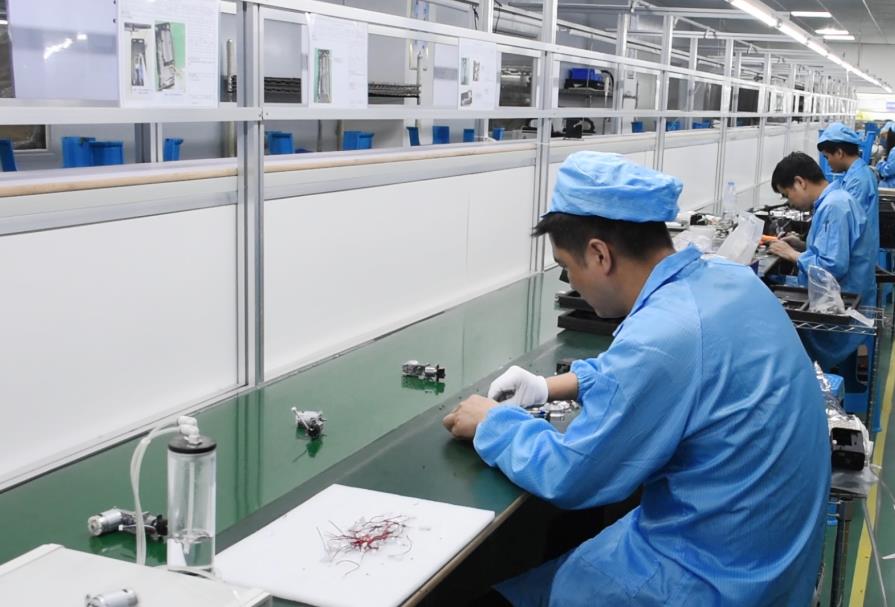
PCB production
We outsource PCB production and strictly control the following quality key points
High quality brand board
Choose the top ranked PCB supplier
Continuously establish supplier relationship management
Capable of completing process capabilities such as 3mil line width line spacing, multi-layer, HDI, impedance, and blind buried holes
All PCBs delivered to our company must undergo 100% electrical testing
Electronic component procurement
100% purchase according to the brand and part number specified in the customer's BOM (unless the customer agrees in writing to purchase alternative materials due to procurement cycle reasons)
Purchasing materials through legitimate channels such as first level agents and top traders
Can provide proof of origin for first level agents
Having a good advantage in centralized procurement, obtaining shorter procurement cycles, the latest material year, and stocking advantages, etc
Provide comprehensive original factory technical support
IQC incoming material inspection
Measure the thickness of the PCB
Check if the through-holes and ink on the PCB are blocked, etc
Check if there is any warping or deformation on the PCB, and if the silk screen is clear
Check if there are any defects such as broken wires, jumpers, etc. on the PCB
Place the PCB in reflow soldering for furnace temperature testing to check for yellowing or deformation
Check if the batch number, part number, and screen printing of the incoming electronic components are consistent with the BOM
Placement of incoming electronic components on bare PCB boards for adaptation testing of solder pads or through holes
Spot check the resistance and capacitance values of incoming electronic components, and compare them with the BOM
Check if there are any scratches, deformations, broken or short feet on the surface of the incoming electronic components
Component storage and solder paste printing
Storage of sensitive components in a professional constant temperature and humidity box
Bake PCB/IC/BGA with strict requirements for 2-12 hours to remove surface moisture and enhance weldability
Using top tier brand solder paste
Issuing high-quality laser steel mesh
Complete procedures for solder paste freezing, thawing, and stirring operations
Equipped with a fully automatic solder paste printing machine, ensuring consistency and reliability of solder paste printing during mass production process
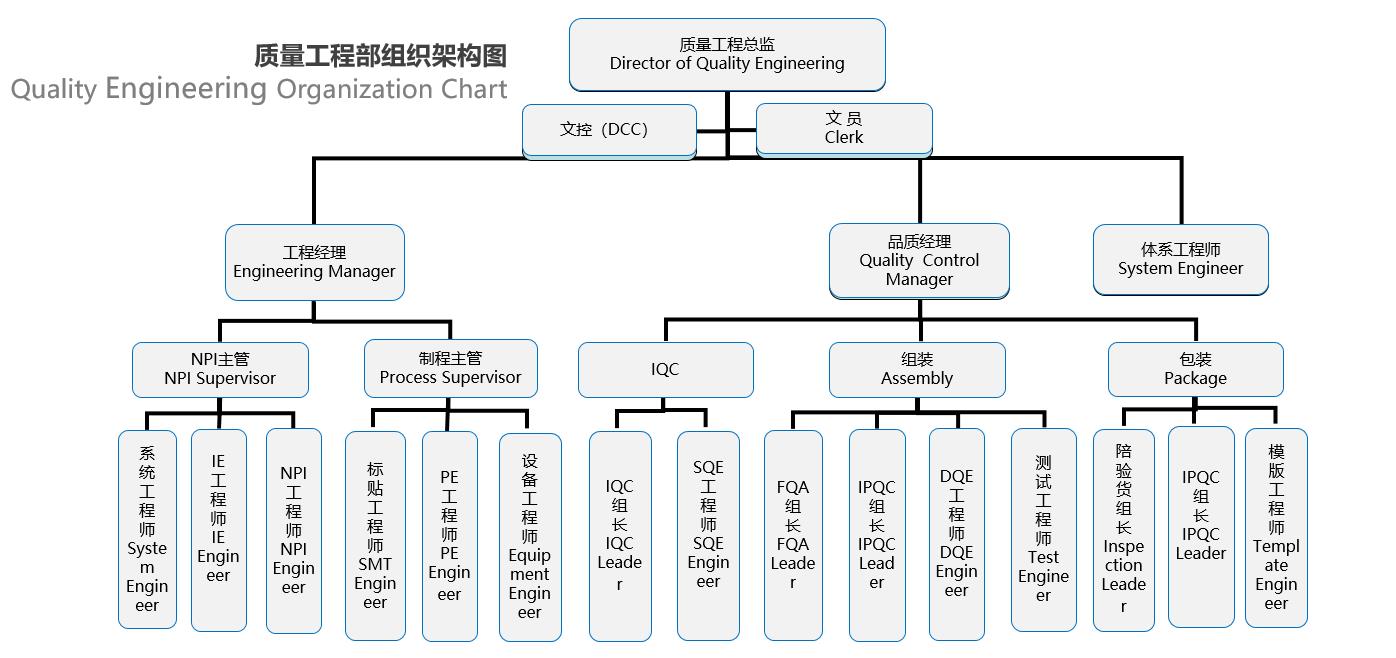
SMT surface mount processing
Adopting YAMAHA YSM20R series high-speed fully automatic SMT mounting machine with an accuracy of 01005
Equipped with electric Feida to reduce material throwing rate and probability of fault warning
Supports mainstream chip types such as QFN, SOP, SOT, TSOP, QFP, BGA, PLCC
YSM20R single machine maximum production capacity 75000 pieces per hour
Equipped with 16 temperature zone reflow soldering and setting a qualified furnace temperature curve
Use a furnace temperature tester every 4 hours to detect and record the furnace temperature
Batch detection of defects such as incorrect parts, missing parts, reverse welding, and virtual soldering using AOI optical detectors
Using x-Ray to prepare a board containing dense ball BGA
DIP plugin processing
Strict workstation operation manual
Issuing wave soldering fixtures for mass production to ensure the reliability and consistency of welding
Using well-known brand wave soldering
Equipped with 4 plug-in production lines to meet the needs of mass production
Equipped with carving machines, the engineering department issues test racks according to customer requirements, and has the ability to complete program burning and functional testing of mainstream chips